
Products
PET Preform
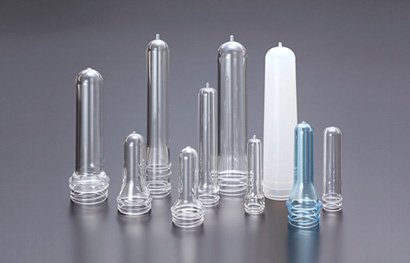
PET Preforms in different shapes
We can provide an efficient concealed cooling system to make PET preform. The machine can avoid them from drooling, which is a new technology. All the services we provide are cost efficiency and help to reduce the client’s budget. Moreover, the customer can design the size and dimension according to the marketing purpose while out engineer will fully support the idea and drawing of PET preform. Because of the flexibility of the PET preform; it can shape into any desire type base on the specification.
The lightweight of the PET preform is another special advantage. It is easy to carry while it is much lighter than the other materials, which can also help to reduce the shipping fee while it is in large amount of shipment. Although it is lighter, the PET preform is still strong enoughto bearing the outside impact. The wall is thinner, which can deduct the weight while it can provide a high strength without breaking easily.
The PET preform can also maintain the cleanness of the environment, because it can be recycle and be reuse. The enterprise will surely prefer it product due to the environment issue is becoming an important matter. It will be popular by the buyer. Even if the PET preform is burned as trash, it won’t produce any poison smelling. The PET preform will be the best choice.
- PET preforms we produced
- 13 gms - 330ml mineral water bottle
- 17 gms - 500ml mineral water bottle
- 30 gms - 1.5 ltrs mineral water bottle
Production Cycle
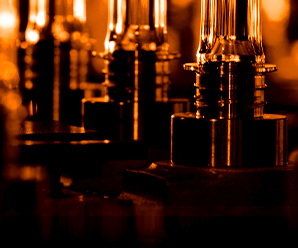
The PET preform, better known as preform, is accomplished through a molding process. The fused PET injected into a mold become a preform, which, by an additional processing step (blowing), takes the form of bottles for beverages for elementary, oil or detergents use. A preform is made by a "finish" (bottleneck), which will not change in the blowing process. "Finish" diameter and thread type are the main features of the preform, features that determine the kind of screw bottle cap and the use of the bottle (for still water, sparkling water, oil, milk).
On the other hand, the tubular structure, will form the bottle in the blowing and molding processes and it determines the basis weights of the final product; diameter, length and shape are the key elements that give the main features to the blown container. The PET polymer, used for the production of preforms doesn't have a colour, it's almost transparent, but once mixed with colouring additives, it can have different shades of colour according to customer requirements.
-
Storage
The polymer is transported in tankers or in Big Bags. The material, once entered into factory, is piped into 19 storage silos from which it's taken depending on the production requirements.
-
Drying of PET
PET, by its nature, absorbs humidity from the atmosphere, in order to give a perfect product, it has to stand to a drying and dehumidification process. The process consists in maintaining the storage silo connected to the feeding of the PET machine for a certain period of time (which may vary depending on the nature of PET from 4 to 10 hours) during this time it's heated with a stream of hot air at a temperature of 170°. The air heating is produced by a system that uses the thermal oil heated by a heat exchanger connected to a group of cogeneration for the production of electric power.
-
Plasticization of the PET
Once dried PET is routed through a screw in the injection chamber. During this phase, the PET is heated to a temperature of about 285° and stands to the lamination phase passing from the solid state (granules) to the liquid state. Before entering into the cochlea the granule can pass through a pre-mixer where it's mixed with a colouring that, with the specific amount, gives the shade as required by the customer.
-
Injection Molding
PET in liquid state is conveyed by the rotating screw in an injection chamber in such quantity as to fill the total cavity installed on the mold. When the mold is closed, the molten PET is injected into the cavities where once in contact with the matrix will solidify and form. The temperatures of cavities and punches are cooled by a system that allows the PET to solidify before being ejected from the mold through a system of extractors.
-
Cooling
The solidification process ends when the preforms are ejected from the mold by a cooled automated gripper.
-
Packing
Once completed the cycle of cooling, the preforms are deposited on conveyor belts and sent in suitable containers called OCTABINS.
-
Handling and Storage
The OCTABINS are taken by an automated system made by 3 AGV shuttles and stored in the warehouse ready to be shipped, a dynamic system that effectively ensures full compliance with the hygiene standards required in the transformation process.